
We are delighted to announce that our workshop Foreman Luke Coxhead has achieved the status of specialist HIAB Diagnostic Engineer and has become our second HIAB Diagnostic engineer, increasing our repair capacity and reducing downtime on servicing and repair jobs.
Three Levels Of HIAB Engineer
How do our Diagnostic Engineers differ from our wider team of other engineers, who are all trained to diagnose faults and do so on a daily basis? The difference is training and experience. In fact, HIAB recognises three levels of engineer.
Every engineer on our team has gone through extensive basic training on HIAB cranes that qualifies them to carry out repairs, maintenance, servicing, LOLER testing and a range of other services. This is the first level, dealing exclusively with hardware.
After a year or so of HIAB experience, an engineer can undertake an additional training course that gives them further product and engineering knowledge. On completion they receive a password to access the HIAB electronic and computerised systems - hence the title of ‘Password Engineers’. These engineers can access software, troubleshoot problems and make repairs, but can’t change the programs themselves or install new programs.
This is the job of the third level; the Diagnostic Engineers. A Diagnostic Engineer is not only experienced with the nuts and bolts of servicing HIAB hardware and software, but has also received training that qualifies them to create new plc programs, create new stability alterations for cranes – and a whole host of other software engineering tasks. It is where a maintenance service moves beyond simply reactive fixing, and into improving your hardware to fine tune performance and increase your crane’s capabilities.
A Valuable Resource
There are only 15 HIAB Diagnostic Engineers in the UK & Ireland, and we now have two of them! The implications for the service we can now offer our customers are huge. Working together, our team of engineers can rapidly diagnose any fault and make whatever repairs are necessary to extend the life of your kit. We can also proactively maintain your equipment to address faults before they become serious, and reduce the risk of unexpected breakdowns. In addition, we can also take active measures to improve the programming of your crane so it works harder and faster at a wider range of tasks.
To find out more about our HIAB authorised services, please get in touch by phone on 0330 999 0003, or by email at service@truckloaders.co.uk.
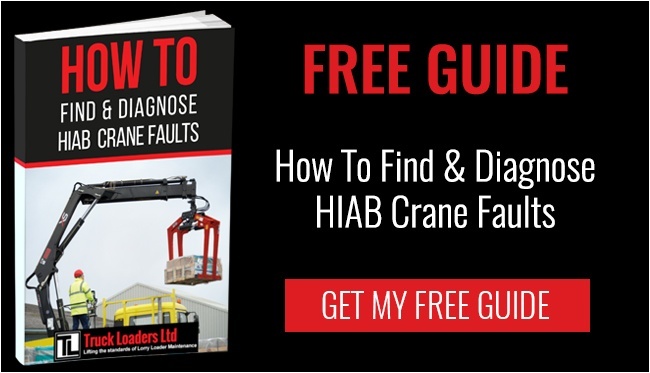